As an Amazon Associate I earn from qualifying purchases through links from this site. See the disclosure page for details.
Recently, I was standing in my workshop wondering which type of welding rod for stick welding you should ideally choose.
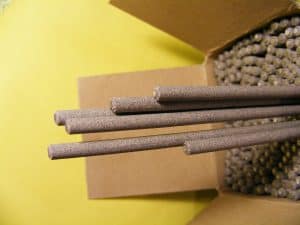
Welding Rods
So I did a recherche. And because I found so much information about welding electrodes, I created this summary.
Below I will show you what stick welding is. Also, you will learn the differences between the most common welding rods. Moreover, I will explain you the encoding of all the digits in the stick electrode AWS classification and what kind of coating material each electrode provides.
Also, you can start your recherche here about which type of welding rod is good for your application.
So let’s start with our first chapter to see what exactly is stick welding.
What is stick welding?
Welding electrodes are consumable welding sticks used for welding projects and machines to weld together metals in the stick welding process.
The stick welding process is also called Shielded Metal Arc Welding (SMAW).
Take a look at the image below to see a typical stick welding setup.
When you do stick welding, you do have a welding machine with an electrode cable and a ground cable. The electrode cable connects the electrode holder with the machine. The ground cable with the ground clamp is attached to the workpiece. The electrode holder holds the welding electrode.

Stick welding setup
How does stick welding work?
Once powered up, electric current flows through the welding rod which creates the arc. During stick welding, the welding electrode is consumed. Because of the heat from the welding arc, metal is liquified and put on top of the base metal (=weld seam).
Shielding gas from the welding electrode helps to avoid oxidation of the metal in the weld pool and makes the welding process more reliable.
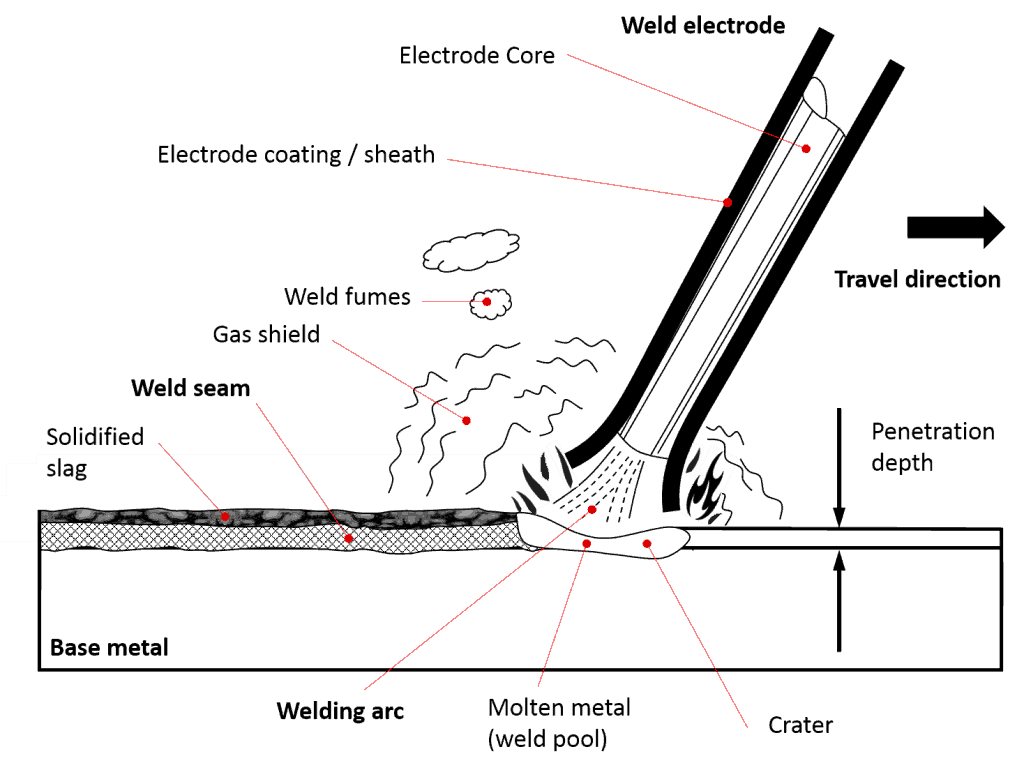
Stick welding with welding rod
Differences in welding electrodes
Welding electrodes differ in the following properties:
- Size (Diameter & Length)
- Tensile strength
- Core material composition
- Coating material composition
- Welding position
Welding rod sizes
Typical rod sizes are 5/64, 1/16, 1/8, 3/32, 5/32, 3/16, 7/32, 1/4 and 5/16 inch. The thicker the rod, the higher your amperage rating has to be. Thus, if you need to weld thin metal sheets, you should also prefer thin welding rods. The length usually ranges between 12″ and 18″.
Take a look at the following tables to see typical sizes of welding rod diameters and lengths in inch and mm.
- Typical Welding electrode diameters
- Typical Welding electrode lengths
Tensile Strength
Tensile strength, which is the ability to withstand a without breaking, is one of the main difference between each rod.
Typically, the tensile strength of each rod can range from 60,000 to 70,000 pounds per inch. Moreover, depending on the number, the rod coating, weld current, and weld seam penetration depth will differentiate.
Welding rod core material
Typically, a welding rod consists of the core wire and an additional flux covering (coating). For example for mild steel covered electrodes, the core wire usually consists of low carbon steel.
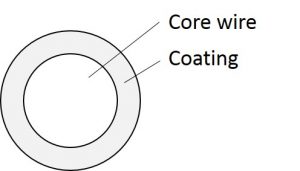
Rod Cross Section
Welding electrode coating
There are 10 main functions of a welding electrode coating. Things the welding rod coating does:
- Prevents oxidation of the welding rod
- Shields the molten metal from oxygen and nitrogen
- Stabilizes the arc
- Shapes the arc stream
- Controls melting rate
- Removes oxides and impurities in the weld pool
- Influences mechanical properties of the weld seam (tensile strength/ductility…)
- Influences welding position (e.g. overhead welding with titanium compounds)
- Provides the slag
- Insulates the core wire (avoids short-circuiting when welding in narrow holes)
Welding position
Many of them can fill any position and are very versatile based on the weld.
Now, take a look at the following chapter, where I will explain to you the different types of welding rods:
back to menu ↑Welding rods classification
According to the American Welding Society AWS, welding rod types are standardized. The AWS classification on rods consists of a letter and four following digits. For example, take a look at the following image:
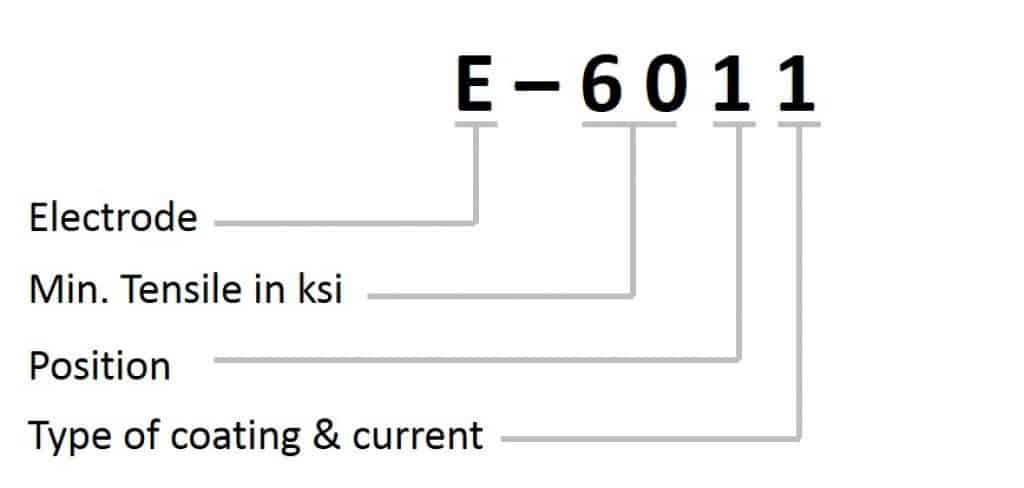
Welding Rod Classification
When you have an E6011 electrode, the letter E corresponds to the Electrode. The 1st and 2nd digit tell you the minimum tensile strength (What is the tensile strength?) your electrode has. In this example, it would be 60,000 pounds per square inch. The 3rd digit tells you suited welding positions. The 4th and last digit gives information about the welding rod coating type and corresponding weld current (AC/DC, DC-, DC+)
If you take most common welding rods and decode the classification information you will receive the following classification list table which contains the type of coating, welding position and the corresponding welding current:

Electrode classification table
DC+ is also called DCEP (=direct current electrode positive) and DC- is also called DCEN (=direct current electrode negative), while AC stands for alternating current.
One thing I’d also like to mention is that moisture resistant electrodes can be recognized by the suffix “R”.
back to menu ↑Typical types of welding rods
Below you will find a selection of well-known welding rods and their typical use-case.
Before selecting the right electrode, you need determine the type of carbon steel you have:
- Low carbon steel: 0.05 to 0.30% carbon content (=mild steel)
- Medium carbon steel: 0.3–0.8% carbon
- High carbon steel: 0.8–2.0% carbon content
In general, increasing carbon content decreases the weldability. High carbon steels require better preparation like pre-heating and post-heating of the welding.
6010 welding rod
Known as one of the most common welding rods, the 6010 welding rod is suited for use with dirty or corroded metal.
In detail, it can deeply penetrate almost any metal and has 60,000 pounds of tensile strength per square inch.
Moreover, the 6010 runs only on DCEP, which gives it a smooth edge. Little slag chips off and the rod strikes easily. Welding decking, penetrating the gauge metal into the beam, is an optimal choice when using this rod. If you don’t have access to an oxyacetylene rig, 6010 makes the job easy with a portable torch. The electrodes burn at a very high speed, which is excellent for welding bridging and joists. This gives the 6010 the advantage over the other rods.
Drawbacks of using this rod include it can only be used with a DC+ current since it has a high cellulose sodium coating. Moreover, the arc can be very tight which makes it hard for new beginners who do not know how to control a tight arc. Also, if it becomes drenched, you may have to purchase a new one since it will be damaged.
Overall, 6010 is a great choice for producing marvelous welds.
6011 welding rod
The 6011 welding rod is another common rod and sometimes mistaken for the 6010 since they are close in perimeter. The 6011 is a great choice for everyday welding applications because it strikes very easily and can be used for many projects such as welding decking. The 6011 welding rod does have wide range of applications, including mild steels, galvanized steels and some low alloy steels. Its tensile strength is 60,000 pounds per square inch.
Moreover, it has an advantage if you have an AC-only machine since it runs on direct current electrode positive (DCEP). This rod does not run on DC- current and does have a high cellulose sodium coating.
Drawbacks include the slag being tougher to chip off and runs less smooth when doing root passes on pipes. 6011 is just as strong as the 6010 and can be used in multiple positions.
6013 welding rod
The 6013 welding rod does have wide range of applications, including low carbon and medium carbon steels, galvanized steels and some low alloy steels.
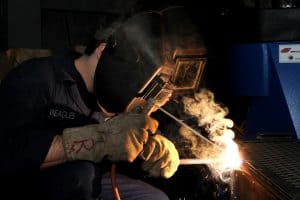
Stick welding with Rod
Typically paired with small, entry-level welding machines, 6013 welding rod is a highly versatile rod that can withstand over 60,000 psi per square inch.
The last 2 digits 13 represent the high titania potassium coating on the electrode, which in return is made easily compatible with DC+, DC- and AC currents. The E-6013 is sometimes called the “all-Purpose” welding rod because it is very versatile. It’s one of the most common used rods in welding schools.
Suited for thinner metals, the 6013 performs light to medium penetration and slag can be removed very quickly. 6013 rods tend to be very clean and visually appealing.
Please make sure to use this type of rod only with clean metal sheets, in contrast to the 6010 and 6011 rods.
On the downside, similar to other rods: When it comes in contact with water, it will become damaged.
7010 welding rod
Developed for welding pipelines, the 7010 welding rod is high cellulose rod that is very versatile and can be used for many positions. It is best suited for vertical up and vertical down welding.
Moreover, the 7010 rod creates a deep penetration that produces a weld puddle that spreads easily with rapid solidification.
It can be used with AC or DC- currents and contains 70,000 psi per square inch. It is perfect for high-pressure applications such as welding carbon-moly piping.
7014 welding rod
THe 7014 welding rod is usually preferred for mild and low alloy steels. Coated in iron powder and titania, the 7014 welding rod is used for shelving, heavy sheet metals, fabrication, and general maintenance.
They reflect smooth beads with ripples. The slag can be easily removed with a slag hammer, often times self-lifting. The 7014 rod provides 70,000 psi. This rod is good for all positions. The iron powder that it’s coated in yields a very high deposition rate. Recommended currents include DCEP, DCEN and AC.
7018 welding rod
The 7018 welding electrode is used for structural welds with low, medium or high carbon steels. The 7018 welding rod produces ductile welds that are very strong. Known for being much smoother and easier than 6011 and 6010 rods, structural welding is most common application with this rod.
Referred as low-hydrogen potassium rods, it is used extensively for factories, shopping centers, dams, bridges, and other high structured facilities. Ship hulls, pressure vessels, boilers and piping are some other typical applications to mention. Versatility comes easy with this rod especially because of the strength (70,000 psi). It can be used with DC+ and AC currents.
Drawbacks include they have to be stored carefully and have to avoid water coming into contact at all costs.
7024 welding rod
Most commonly used in flat and horizontal positions, the 7024 welding rod has good weldability and is excellent for ships, railcars, truck bodies, and barges.
This rod is ideal for weld penetration with little root porosity. Laying down lots of weld metal is made easy with the 7024. The rod produces smooth welds and the slag comes off easily. They are intended to be used with AC or DCEP/DCEN currents.
Drawbacks include high heat input and these rods are only good for flat and horizontal positions.
Picking the right welding rod – video guide
For even more in-depth explanation take a look at the following video provided by Kevin Caron:
back to menu ↑How to handle welding electrodes
Don’t bend welding electrodes
Some welders or beginners bend their welding electrodes to shorten them or to improve welding position.
This is very wrong, please don’t do this.
When bending the electrode, the coating gets damaged. This will harm your weld results.
How to store welding rods?
In general, most stick welding rods are sensitive to moisture. That means, stick electrodes take up moisture from the air.
Low hydrogen stick electrodes that pick up moisture can lead to hydrogen induced cracks.
Correct storage of welding rods is crucial in order to guarantee quality weld seams. When welding with “wet” electrodes, porosity and hydrogen induced cracks can occur in your weld seam.
If you have a low hydrogen stick electrode you should leave it in its original packaging. Once the packaging has been opened, you should store it in a oven at 250 up to 300°F.
Moisture resistant electrodes have a trailing “R” suffix in their AWS classification code. Although even moisture resistant electrodes may only exposed to the environment for up to 9 hours.
Source: https://www.lincolnelectric.com/en-us/support/welding-how-to/pages/storing-electrodes-detail.aspx
How to redry low hydrogen stick electrodes?
Some electrodes that have been exposed to moisture can be re-dried in a special drying oven.
Once these electrodes pick up moisture you should redry them in your rod oven. For this take the electrodes out of the can and spread them in the oven. Leave them at least for one hour in the oven to make sure the electrodes reach the required re-dry temperature.
Depending on the electrode type, different re-dry parameters have to be applied. Some electrodes have to be pre-dried at lower temperatures before final drying them to minimize cracking of the coating.
back to menu ↑Summary
To sum it up, welding rods can be used for multiple projects. Some are better suited for a simple DIY project with less penetration depth while others are better suited for high output currents for thick steel bars. The right welding rod makes your welding process easy and smooth. Every rod listed above has its ideal application.
Do you have any further experience that you would like to share here? Please don’t hesitate and leave a short comment below.
Image Credits: Pixabay / byrev, 263509670 / Shutterstock, Pixabay / Skeeze, anarosadebastiani / Pixabay
what happens whens the electrode coating is damaged or wet ?
Hi Johan, good question. In my experience, you should avoid damaged coating as well as wet coating.
When the have too much moisture, this can lead to porosity or cracks. Moreover its more difficult to weld with wet electrodes (unstable weld process).
A damaged coating can cause porosity, too. Undercuts or lack of penetration are also often an issue when welding with wet electrodes.
I have a UTV (mule) that the frame got broke. I am going to weld it back; I plan on using the 1/8″ 6011 rod. I have been told to knock all the flax off of the rod before I start.